Catalyst innovations drive more performant and sustainable refining and petrochemical industries
- Zeopore
- Apr 22, 2021
- 6 min read
Better zeolite catalysts enhance today's oil refining and petrochemical processes, and pioneer biobased manufacturing and chemical plastic waste recycling
This article on Zeopore is published in the following (inter)national media. Most logos are clickable to forward you to the respective publications:
Zeopore successfully builds on groundbreaking research at KU Leuven (Belgium), which focused on advancing mesoporization technology and the economical applicability of mesoporized zeolite catalysts. Today, Zeopore makes current processes in oil refineries and petrochemical plants more performant, sustainable and cost-effective. It offers proven catalytic benefits for key industries including FCC, hydrocracking and dewaxing, which result in more efficient operations and huge financial benefits. Zeopore's zeolite innovations also serve as the fundament in new emerging applications such as the conversions of biomass or waste plastics. After having increased its capital in August 2020, Zeopore is further strengthening its technological position and collaborating with reputable parties towards scaleup and commercial rollout.
Superior zeolite catalysts manufactured at low cost
In the refining and petrochemical industry, zeolite catalysts are widely used to produce the desired automotive fuels and petrochemical base chemicals in an efficient and sustainable manner. Apart from their excellent intrinsic properties (e.g. stability, crystallinity, acidity), these catalysts exhibit a narrow micropore structure that forms the basis of their strength, yielding exceptional selectivities to desired products. However, such narrow pores also provoke access and diffusion limitations. As a result, only a minor part of the intracrystal surface of zeolites is actually utilized.
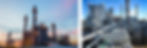
"To resolve this, zeolites are 'mesoporized' to further increase catalytic efficiency by improving their porous structure," says Kurt Du Mong, CEO of Zeopore. "Complementing the zeolite's micropores with a network of larger mesopores, significantly increases the accessibility to the active sites inside the zeolite crystals. Moreover, by tuning the porosity and other zeolitic properties, one can steer the selectivity and improve the stability performance of the catalyst for each individual process.”

For decades, mesoporous zeolites have been renowned for their outstanding catalytic performance. However, they have been commercially overlooked based on the high price tag and limited applicability of the processes required to produce them on a large scale. In 2015-2017, groundbreaking research by Dr. Danny Verboekend at the KU Leuven Center for Surface Chemistry and Catalysis under supervision of Prof. Dr. Bert Sels, solved the problem. Danny Verboekend: "Our processes convert standard commercial zeolites into superior materials, using post-synthetic treatments in aqueous solutions in combination with steam. Our know-how and technologies enable to couple the benefits of high-quality accessible zeolites with a low-cost and tunable manufacturing process."
The potential was clear and in December 2017, Zeopore was founded with Kurt Du Mong as CEO and Danny Verboekend as CTO. Today, the team has grown into a balanced workforce that combines decades of accumulated experience and covers all key disciplines of the business, including technology, quality, upscaling and commercialization. "It is also beneficial to be located in Leuven, Flanders (Belgium), the largest petrochemical cluster in Europe."
Leuven serves as the perfect ecosystem for Zeopore to further grow and excel. In 2020, the city was awarded 'European Capital of Innovation' by the European Commission and its university heads Europe's list of most innovative universities. Also in 2020, Zeopore substantially increased its capital through an investment round led by Capricorn Partners with participations and continued support from existing shareholders KU Leuven, Innovation Fund and Gemma Frisius Fund.
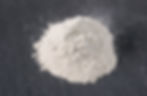
Unique technology platform for zeolite catalyst development
Over the past three years, Zeopore has created a unique technology platform to cost-effectively make more performant zeolites with custom-made properties. Next to a larger output of desired products, this leads to higher product quality, lower energy use, and less waste for several catalytic processes. Why is Zeopore's technology platform so revolutionary?
Applicable to any commercially relevant zeolite type
Zeopore's innovative technology platform allows to convert any commercially and readily available zeolite into a high-quality mesoporous zeolite at an affordable price. This compares favorably to other -expensive- methods that are only applicable to one or a few zeolite types. Especially in widespread faujasites or pentasils, Zeopore has built a broad database of mesoporisation treatments, but it can also handle more exotic zeolitic species such as chabazite (e.g., SSZ-13) or zeolite-like silicoaluminophosphates (SAPO’s).

Broad tunability of desired zeolitic properties
Zeopore's technology toolbox is used to produce zeolites with a tunable mesoporosity in accordance with the targeted refining or petrochemical process. We are able to deliver the porosity profiles and acidity levels that are optimal for any custom application, as well as embed catalytic metals into the zeolite in the post-synthetic process.
Retained intrinsic properties
While establishing the required mesoporization, Zeopore is able to preserve or even boost other critical intrinsic zeolitic properties including microporosity, (hydrothermal) stability, crystallinity and composition. Often other mesoporisation techniques partially destroy the powerful properties of a zeolite.
Increased economics and scalability
The applied mesoporization methods at Zeopore only require standard unit operations and low-cost ingredients, which are specifically designed to maximize mesopore formation quality and efficiency. Therefor its processes are highly scalable and cost-effective, thus preserving the economic character of zeolites in industrial applications.
Proven catalytic benefits across a range of markets
By systematically removing hurdles up-front in the synthesis and scale-up of mesoporous zeolites, Zeopore has reached a unique technological position. Verboekend: "We have developed and patented several specific technologies to avoid commercialization pitfalls such as the use of costly organics, the excessive loss of precious zeolite, complex separations technologies, and low reactor productivity. In doing so, Zeopore offers catalyst manufacturers up to a 10-fold cost advantage compared to competing technologies."
Zeopore offers proven catalytic benefits in key applications across markets. In fluid catalytic cracking (FCC), mesoporized zeolite catalysts increase the yield of middle distillates like diesel or jet fuel, and deliver more light olefins for further petrochemical processing, such as propylene and butane isomers. When looking at hydrocracking applications (HDC), more middle distillates as well as higher conversions and lifetime are obtained. In dewaxing, mesoporized zeolite catalysts lead to significantly higher degrees in iso-selectivity and reduce losses to lights for both fossil fuel and bio-renewable feeds.

Behind such nano-scale chemistry lies an enormous economic potential. Catalysis makes up less than two percent of the cost of refining, but they have a major impact on the overall efficiency. Therefore, each improvement of the catalyst provides great added value. "Our cost-effective manufacturing of highly porous zeolites translates into benefits amounting to 30-50 million dollars per year per installation," calculates Du Mong. "Worldwide there are almost a thousand crackers, which refine crude oil into usable products. This way, Zeopore is on the verge of opening a global market of more than 30 billion dollars. But equally important is the more efficient use of valuable feeds, such that Zeopore contributes to a sustainable industry."
Pioneering bio fuels manufacturing and chemical plastic waste recycling
Zeopore's innovation for higher-performance cracking of distilled oil fractions also serves as a fundament in current emerging applications. Zeopore’s technologies are enabling components in attaining an efficient catalytic conversion of complex feedstocks such as biomass or waste plastics. In this field, we actively contribute to an alternative to fossil fuels and the integrated chemical recycling of polymer waste streams. Prof. Dr. Bert Sels, a co-founder of Zeopore, is an international authority in biomass conversion.
Du Mong: "Overall, Zeopore ensures a higher degree of sustainability and environmental, social governance (ESG) in both fossil fuel and emerging supply chains." The superior mesoporised zeolites of Zeopore increase the process efficiency, which translates into energy savings and a better usage of valuable feeds or additives. In chemical plastics recycling, Zeopore pioneers the catalytic valorization of waste plastics as a more valuable alternative for incineration, which reduces CO2 emissions and residual waste.
Continued innovation and evolving towards industrial rollout
Where does Zeopore stand today? "Currently, Zeopore is collaborating with reputable parties on multiple applications in different markets," says Du Mong. "We are gradually shifting from demonstrating the added value of tuned mesoporized zeolite catalysts to industrial scale-up and commercialization in collaboration with leading international parties. In this regard, we are exploring commercialization through technology licensing or product supply business models."
Du Mong concludes: "The next phase in Zeopore's future roadmap is to customize our manufacturing processes to the industrial demands of our partners, to allow for industrial runs and commercial rollout. In parallel we further strengthen our technology position by developing deeper insights into the link between (mesoporised) zeolitic properties and its catalytic benefits to get the maximum out of our versatile technology platform. We are ready to drive a more performant and sustainable oil industry, pioneer bio fuels, and move the needle in chemical plastic waste recycling."